László Rátkai,a Tamás Pusztai,a László Gránásy,a,b
a Wigner Research Centre for Physics, P.O. Box 49, H-1525 Budapest, Hungary
b Brunel Centre of Advanced Solidification Technology, Brunel University, Uxbridge, Middlesex UB8 3PH, UK
Casting methods are widely used for producing metal components. The cast product solidifying in the mold is usually polycrystalline, i.e., it is composed of a large number of crystallites. Its mechanical and other properties are determined by size-, shape-, and composition distributions of the crystallites, known as the microstructure. The melt flow and the motion of the growing crystallites play an essential role in determining the microstructure that evolves in casting: the temperature distribution and the variation of the solidification velocity leads to a transition between the columnar dendritic (fern leaf-like) crystallites growing from the wall of the mold and the crystal nucleation dominated equiaxed dendritic solidification morphology. This morphological transition is influenced by the melt flow partly via modifying the composition distribution ahead of the solidification front, partly by rearranging the crystal particles formed in the equiaxial domain. As these phenomena influence the microstructure of the cast parts, and thus their mechanical properties and failure characteristics, a detailed understanding and controlling of these processes is of pronounced practical importance. Computer modelling is expected to play an important role in the realizing of these.
In a recent article that appeared in the Nature partner journal – Computational Materials (impact factor: 9.20), László Rátkai, Tamás Pusztai and László Gránásy, physicists from the Wigner Research Centre for Physics report on developing of a computer model capable of modeling the flow aspects of the columnar to equiaxed transition. The proposed computer model is based on combining the phase-field theory of solidification with the lattice Boltzmann technique for simulating melt flow. To handle mobile particles, an overlapping multigrid scheme was developed, in which each individual crystal particle has its own grid moving with the particle. The equations describing the growth of the crystal particles are solved on their own grids, and are moved according to the lattice Boltzmann equations solved on a global grid. Using this approach, the researchers were able to model two possible modes of columnar to equiaxed transition in an Al–Ti alloy important for aerospace and automotive applications.
The abilities of the developed model are illustrated by Fig. 1 and the computer animations:
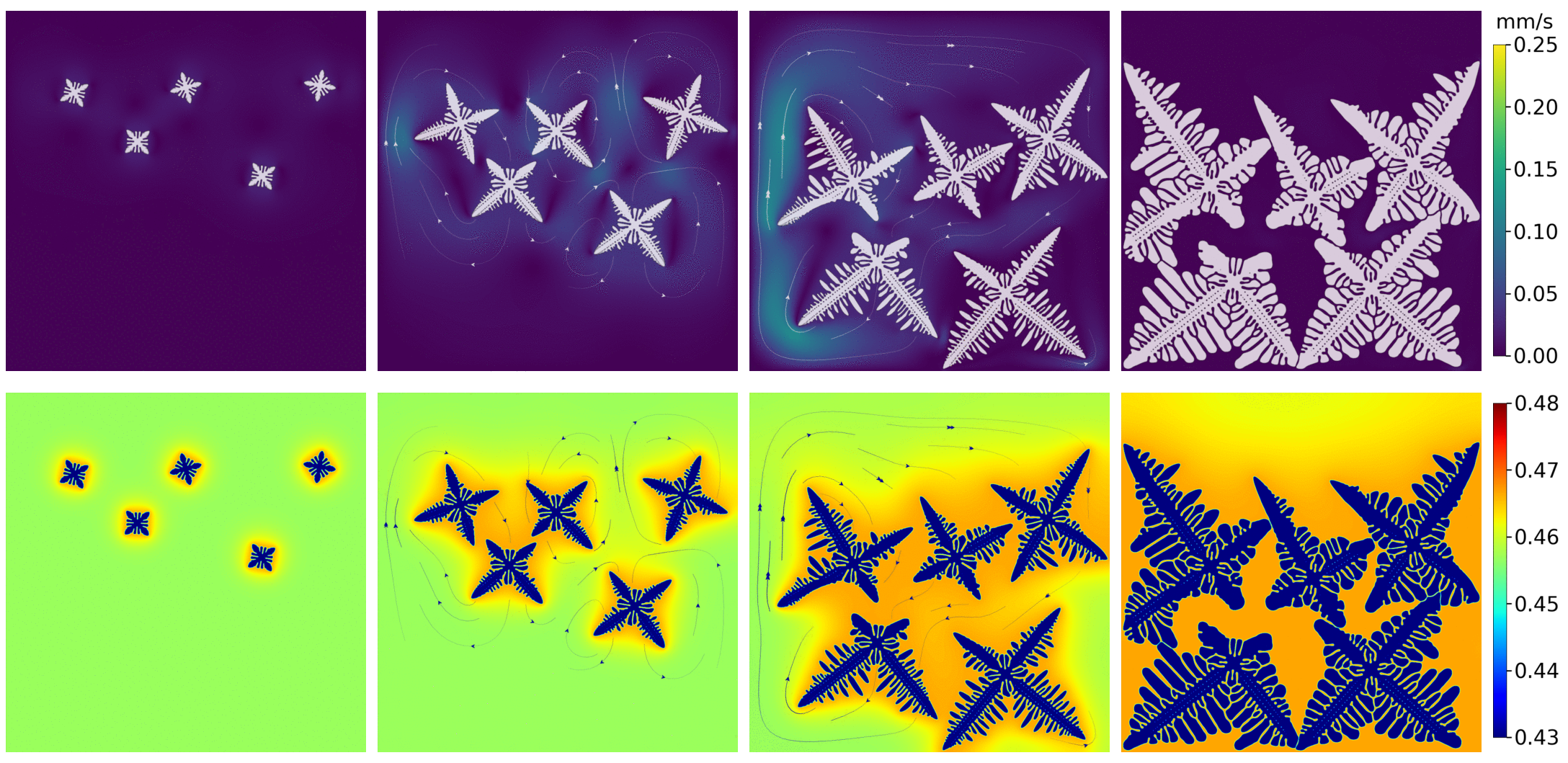
Fig. 1: Snapshots displaying the velocity and concentration fields (upper and bottom rows, respectively) with streamlines during the sedimentation of growing dendritic particles in molten Al-Ti alloy under gravity. Time increases from left to right. The simulation was performed on a 2000 × 2000 grid and a single GPU card.
Animations: Computer animations showing the velocity and concentration fields (left and right, respectively) during columnar to equiaxed transition via columnar growth from the bottom and nucleation in the upper domain of the simulation box. The simulation was performed on a 4096 × 3072 grid and a single GPU card.
Link to the original paper: https://www.nature.com/articles/s41524-019-0250-8
This work was supported by the "Frontline" excellence programme of the National Research, Development and Innovation Office (NKFIH, Hungary) under contract no. KKP-126749. Early stage model development was supported by the NKFIH under contract K-115959, and by the ESA Microgravity Application Programme project “GRADECET”.